Компания «Лазерные системы» из науки шагнула в прикладной мир бизнеса, создав первые официально признанные отечественные 3D-принтеры по технологии селективного лазерного сплавления металлов (SLM)
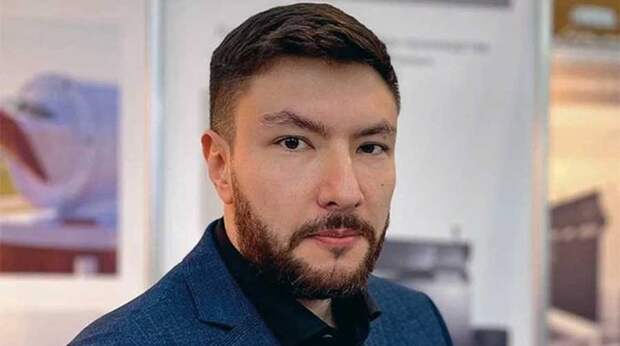
Компания «Лазерные системы» из науки шагнула в прикладной мир бизнеса, создав первые официально признанные отечественные 3D-принтеры по технологии селективного лазерного сплавления металлов (SLM)
Удивительно слышать, как это объемное сооружение размером с жилую комнату называют «принтер», но это он и есть, только промышленный вариант, предназначенный для выращивания деталей и узлов из порошков металлов методом 3D-печати.
Создан он в России, в стенах компании «Лазерные системы». У него русские «мозги», то есть программы, его проектировали петербургские инженеры и конструкторы. И даже собран он, по заключению Минпромторга, на 75% из комплектующих российского производства, набрав максимальное количество балов в соответствии с 719-м постановлением правительства.Статья по теме: Быстрее, выше, сильнее: как 3D-технологии меняют обувь
Сторонний наблюдатель может подумать: ну вот же, могут сделать, кода захотят! Вот оно, импортозамещение в действии! На самом деле в «Лазерных системах» с лазером на «ты» очень давно, ведь компания создавалась еще в 1990-е как научно-производственное предприятие группой ученых и инженеров на базе Балтийского государственного технического университета (БГТУ) «Военмех» им. Д. Ф. Устинова. Долгое время предприятие возглавлял Анатолий Борейшо, доктор наук, один из разработчиков отечественных лазерных систем летательных аппаратов. Вплоть до 2015 года основными задачами компании были НИОКР, выполнение госзаказов для разных министерств и частных клиентов. И только построив на территории особой экономической зоны технико-внедренческого типа «Санкт-Петербург» высокотехнологичный производственный комплекс площадью 6000 кв. м, компания начала расти как реальное действующее производственное предприятие, способное серийно выпускать оригинальные продукты собственной разработки.
Компания «Лазерные системы» создана 1998 году в Санкт-Петербурге. Специализируется в производстве промышленных 3D-принтеров и алкорамок (средства оперативного контроля персонала на предмет употребления алкоголя для крупных промышленных предприятий). Производственный комплекс общей площадью свыше 6000 кв. м расположен на территории ОЭЗ «Санкт-Петербург».
Число сотрудников — 300 человек.
Выручка — 1 млрд рублей.
В портфеле наукоемкой компании имеется большой запас идей и компетенций, но вот какие из них выводить в люди — диктует уже рынок. О том, как «Лазерные системы» подхватили тренд на развитие аддитивных технологий, параллельно разработав собственную программу обучения кадров для обслуживания этого сложного оборудования, о создании облакомеров и лидаров для машинного зрения, а также о неожиданной роли компании в борьбе за трезвость рабочего класса в России, «Моноклю» рассказал директор департамента аддитивных технологий компании Алексей Ким.
— Рынок аддитивных технологий в России показывает бурный рост, вызванный прежде всего потребностью предприятий в замещении запчастей к импортному оборудованию. А как вы на него пришли, когда начали выпускать 3D-принтеры по технологии SLM?
— Аддитивными технологиями в части селективного лазерного сплавления металлических порошков, она же SLM (Selective Laser Melting), мы начали заниматься с 2016 года, когда наша компания взяла ниокровскую работу по созданию неких технологий для 3D-печати: нанесения металлических порошков, сплавления металлических порошков с помощью лазерного излучения и так далее. Мы эту научную работу успешно реализовали, накопили большое количество компетенций и задумались: а что с этими знаниями делать дальше? Положить в стол как задел на будущее или же попытаться создать рыночный продукт, 3D-принтер, который будет иметь какую-то коммерческую значимость? Пошли по второму пути, начали эти компетенции инициативным порядком для себя развивать и в итоге в 2017 году разработали наш первый 3D-принтер, который, кстати, до сих пор у нас работает.
Естественно, мы ориентировались на известных западных производителей в части технических решений, которые там применялись: анализировали их, довольно глубоко изучали. Но наш принтер не копия западного, это машина в своем роде уникальная, самодостаточная и полностью разработанная нами. Во всех наших принтерах, которые давно выпускаются серийно, все решения — собственные как в части программного обеспечения, так и в части технического воплощения — разработки, изготовления, поставки.
До 2022 года аддитивное направление, в частности SLM-оборудование отечественного производства, было не очень популярно, так как на рынке присутствовали представители европейских и американских компаний — EOS, SLM, Concept Laser, Trumpf, 3D Systems и других. Собственно, эта технология из Европы и пришла, не мы ее придумали. Поэтому спрос на отечественное оборудование был крайне незначительным, присутствовал некий скепсис до февраля 2022 года. А потом произошли известные события, и в течение нескольких месяцев конъюнктура рынка очень сильно изменилась, потому что все западные производители в этом сегменте ушли с нашего рынка, буквально в течение первого месяца все разбежались. Но промышленность SLM-технологию уже успела пощупать, успела в ней заинтересоваться. И с того времени, со второй половины 2022 года, мы уже видим большой интерес к отечественной продукции.
— Китайское аддитивное оборудование разве не конкурент для вас?
— На рынке присутствует азиатское оборудование, китайское, но с ним тоже есть трудности. Во-первых, многих останавливает качество такого оборудования, а во-вторых, проблемы с сервисом. Гораздо удобнее иметь дело с производителем в России — это склад запчастей, оперативная поддержка, контроль качества, обучение специалистов заказчика производителем. Это и есть козыри отечественных производителей, в частности наши. Да и по цене мы с Китаем хорошо конкурируем, в зависимости от модификации и комплектации где-то на десять-двадцать процентов дешевле можем быть. Плюс ко всему рынок, испуганный уходом западных поставщиков, теперь настороженно смотрит и на Китай — как бы он не стал второй Европой, ведь вторичных санкций там боятся. А для нас это окно возможностей, мы стремимся максимально много сделать сейчас. Да, SLM-технология сложная, дорогая, тяжелая, но эффективная и в ряде случаев незаменимая, уникальная.
— А в чем ее уникальность?
— Вот я вам сейчас покажу наиболее яркие образцы деталей, полностью напечатанные на металлическом 3D-принтере. Вот это изделие в готовом виде имеет закрытую цилиндрическую форму, но мы электроэрозией вырезали из него сегменты, чтобы показать внутреннюю структуру. Это смесительная головка жидкостного реактивного двигателя, изначально ее собирали из 105 деталей, а в своей трудоемкости производство изделия составляло порядка тысячи часов. Нам удалось оптимизировать процесс, сделать изделие единым, цельным, по сути одной деталью, сократив трудоемкость примерно в десять раз. На срезе видно, насколько сложна структура этой смесительной головки, какие тонкие здесь каналы, поры.
Или вот еще посмотрите на это изделие в разрезе — на горелку газотурбинного агрегата, которую мы сделали совместно с крупной газодобывающей компанией в рамках импортозамещения. Так вот, эти изделия невозможно изготовить никаким методом, кроме аддитивного: ни отливкой, ни фрезеровкой, ни токаркой — только вырастить. Если мы будем отливать деталь, а это самая близкая технология к изделию, то никогда не сможем из полостей удалить остатки формы, они так и останутся. Вот для таких случаев, для изготовления особо сложных изделий, которые невозможно создать иначе либо нецелесообразно делать с помощью других технологий, аддитивная история подходит лучше всего. Она здесь имеет и самую большую финансовую, экономическую эффективность.
Однако это вовсе не означает, что аддитивные технологии подходят только для выпуска сложных изделий, можно производить и относительно простые детали, правда, им будет сложнее выдерживать конкуренцию с традиционными методами производства, с классической мехобработкой или литьем, но можно и конкурировать, если речь идет о мелких сериях. Дело в том, что аддитивная технология —производство небыстрое, производительность не очень высокая ввиду физики процесса. Но зато, если вам нужно изготовить какой-нибудь волновод в штучном экземпляре, это лучшее решение. Потому что классический метод изготовления волновода предусматривает создание сложной технологической оснастки, которая стоит дорого. В итоге и сам волновод получается дорогим. А в аддитивной технологии оснастка вообще никакая не нужна, у нас просто деталь вырастает. И для таких историй, как антенны, рупорные конструкции, полотна ФАР (фазированные антенные решетки. — «Монокль»), волноводы, прочая СВЧ техника, аддитивная история тоже подходит, потому что эта продукция чаще всего либо мелкосерийная, либо штучная.
Иметь свой 3D-принтер выгодно, но не всем
— А что по расходам эффективнее для бизнеса — покупать оригинал зарубежной детали или заниматься реверс-инжинирингом, то есть самостоятельно создавать копии изделий по существующему образцу?
— Оригинал, опять же, купить негде, это санкционная продукция, а если и найти, то срок поставки альтернативы оригинального изделия может составлять от двух до пяти месяцев и доставка будет дорогая. На 3D-принтере срок изготовления сложной детали в среднем неделя, а себестоимость получается невысокая. Приведу в пример интересный коммерческий случай. Одна крупная металлургическая компания еще до начала санкционного давления прорабатывала возможность печати деталей для своих прокатных станов методом аддитивных технологий и пришла к следующим выводам. Оригинальная запчасть у них работает, условно, два месяца, а стоит полторы тысячи евро. И эти запчасти надо постоянно иметь на складе. Если же печатать эти запчасти самостоятельно на 3D-принтере, то даже при условии, что они эксплуатировались бы не два месяца, а две недели, их было бы выгодней выпускать, так как за две недели можно напечатать под сотню таких деталей. Компания приняла решение погрузиться в аддитивную технологию и до сих пор печатает запчасти для своего оборудования на нашем принтере. Так что да, одно из направлений использования аддитивных технологий — это реинжиниринг, или обратное проектирование.
При этом надо понимать, что SLM-технология, интересная и перспективная, не панацея для всех, так как она новая, сложная, дорогая и вряд ли в ближайшее время станет дешевой, как это было с 3D-принтерами для пластика, которые буквально через три года превратились из дорогой игрушки в ширпотребный товар, его сейчас можно поставить на любой подоконник. С SLM-технологией в ближайшее время такого не случится, хотя мы уже сейчас видим, что она дешевеет и все более широкие массы людей к ней, скажем так, приобщаются.
Сложности ее применения заключаются в том, что для качественной печати надо обладать специальными навыками, знаниями — быть хорошим конструктором, инженером, металлургом, технологом, ну и должны быть операторы, умеющие на этом оборудовании работать. То есть порог вхождения в технологию весьма высокий, не каждое предприятие может себе это позволить. И это дорогое оборудование, цены даже на маленькие 3D-принтеры находятся в диапазоне 10‒20 миллионов рублей, а большие принтеры, позволяющие печатать изделия размером 200‒300 миллиметров, стоят десятки миллионов. Очень большие принтеры, с возможностью печати деталей больше 400 миллиметров стоят за сотню миллионов рублей. Кроме того, номенклатура изделий, подходящая под SLM-технологию, не столь обширна. Но если компания имеет в своем производстве очень сложные позиции и испытывает трудности в их производстве традиционными методами, то там аддитивные технологии приживаются хорошо.
— Какие материалы используются для печати деталей по SLM-технологии и где их можно приобрести?
— Для SLM-технологии перечень материалов широко известен в узких кругах. Это большое количество нержавеющих сталей, их там порядка десяти-пятнадцати наименований. Это жаропрочные никелевые сплавы, то есть инконели: ВЖ-159, ЭП-648 и прочие. Это титановые порошки ВТ-6, ВТ-1.0 и некоторые другие. Это биосовместимые кобальт-хромовые сплавы для протезов, зубов, костей и так далее. Это алюминиевые порошки РС-300, РС-533, РС-553 и другие. Вот сейчас у нас есть задача научиться работать с порошком чистой меди. Дело в том, что при сплавлении чистой меди возникают сложности, потому что в спектральном диапазоне того излучения, которым мы сплавляем наши основные материалы, она имеет очень высокий процент отражения, поэтому плохо сплавляется традиционными методами. Мы сейчас работаем над тем, чтобы сформировать режим сплавления медных сплавов и чистой меди в том числе, и уже имеем некие наработки и успехи.
Что касается страны происхождения материалов, то мы изначально ставили себе задачу научиться работать с российскими порошками, и мы это сделали, хотя на нашем рынке представлены и другие порошки. В стране практически все эксплуатанты 3D-принтеров пользуются отечественными порошками, потому что они пристойного качества и их производителей тоже хватает, порядка полутора десятков компаний можно назвать.
— Деталь из порошка металла… В какой момент она набирает прочность, как это происходит?
— Что касается физики процесса, то это послойное сплавление, по сути литье, только без формы и с прямым подводом энергии в виде лазерного луча. В принтере есть ростовой стол, туда насыпается тонкий слой порошка, у нас это 30 микрон. И лазерный луч, пробегая по определенной траектории, этот порошок сплавляет. Дальше стол опускается вниз, насыпается следующий слой, таким образом формируется объем порошка. И следующий слой приплавляется лазером к предыдущему. И так, слой за слоем по 30 микрон, у нас вырастает изделие. Что касается его однородности, то для хорошо отработанных режимов сплавления мы достигаем относительной пористости в материале на уровне существенно ниже одной десятой процента, пористости практически нет. И по этому показателю изделия приближаются к литью под давлением, то есть они сплошные. Не надо думать, что напечатанное изделие какое-то пористое, нет, оно по пористости может быть лучшего качества, чем традиционное литье. И по физико-механическим свойствам изделие соответствует паспорту на материал после нормализующего термического отпуска. Так что в части физмеха, если хорошо отработан режим и установка исправна, изделия получаются прочные и надежные.
— В каких отраслях аддитивные технологии востребованы больше всего?
— В первую очередь речь идет об авиации, в частности об авиационном двигателестроении. Не секрет, что контур Объединенной двигателестроительной корпорации активно занимается высокотехнологичными аддитивными технологиями, наверное, они в России одни из самых активных пользователей. Но здесь имеются трудности с нормативной базой, ведь просто так поставить напечатанное изделие в самолет нельзя, надо пройти соответствующие процедурные сертификации. И это отдельная история, которая дополнительно усложняет развитие аддитивных технологий.
Много запросов из космической отрасли, где требуются разные сложные продукты. Там основная проблема связана со снижением массы изделий, ведь в космосе каждый грамм полезной нагрузки, выведенной на орбиту, стоит больших денег. Определенными инженерными методами можно из тяжелой детали получать деталь такую же по прочности, по своим физическим свойствам, но легче в полтора-два раза, а может, и больше. И когда идет расчет эффективности приобретения 3D-принтера для таких целей, использование SLM-технологии оказывается выгодным.
— Если компания не может себе позволить приобрести промышленный 3D-принтер, да и запроса на его регулярное использование нет, а импортозамещающие детали нужны, как быть?
— Вот мы тоже в определенный момент об этом задумались. Сначала только производили на продажу 3D-принтеры, а совсем недавно, в апреле этого года, официально открыли у себя Центр аддитивных технологий, то есть вышли на рынок оказания услуг по печати деталей. На самом деле такой запрос был давно, по моей оценке, да и не только по моей, потребность в услугах печати деталей в несколько раз превышает все производственные мощности по стране. Только открыв свой Центр аддитивных технологий, мы почти сразу законтрактовали все машины на несколько месяцев вперед, даже рекламу не давая. Как правило, печатаем запчасти к иностранному оборудованию, которое стоит по всей стране. И здесь просто поле непаханое, это насущная проблема сейчас. Ведь есть оборудование на предприятиях, стоимость простоя которого, месячного или даже недельного простоя, сопоставима со стоимостью нового оборудования. Поэтому заказчики всячески заинтересованы в том, чтобы их заказ быстро выполнили.
Да и не всегда дело упирается только в деньги: чтобы хорошо печатать детали, надо иметь соответствующие компетенции, понимать принципы аддитивного производства. Этих кадровых ресурсов тоже не на всех предприятиях хватает, что повышает порог вхождения в технологию.
Кадры на вес золота
— То есть все упирается в кадры?
— Да, совершенно верно. И это один из вопросов, которые необходимо решать в масштабах страны, если всерьез ставить задачу развития аддитивных технологий. Нужен кадровый потенциал, люди, которые умеют проектировать подобные вещи, а они сейчас на вес золота. И это тоже один из стопоров, кроме отсутствия нормативной базы, на пути повсеместного внедрения этой технологии.
Только открыв свой Центр аддитивных технологий, мы почти сразу законтрактовали все машины на несколько месяцев вперед, даже рекламу не дава
Что касается вклада «Лазерных систем» в процесс подготовки кадров для отрасли, то мы практикуем глубокое обучение специалистов заказчика. Можно сказать, что вместе с поставкой оборудования мы принудительным образом обучаем у себя кадры, потому что считаем это необходимым. Надо отметить, что заказчики охотно идут навстречу в этом вопросе, ведь мы учим их сотрудников работе на оборудовании, даем знания по основам технологии, как физическим тонкостям, так и практическим, чтобы установка скорее начала выращивать что-то полезное, а не просто тестовые детали.
— А где ваша компания набирает кадры такого уровня? Кто занимается подбором специалистов в команду?
— Как руководитель департамента аддитивных технологий, в том числе и я этим занимаюсь. Кроме меня в департаменте работают еще порядка тридцати человек, почти половина из них — инженеры-конструкторы, которые разрабатывают новое оборудование помимо того, что уже выпускается серийно. Кстати, не так давно мы разработали маленькую установку начального уровня М150 — 3D-принтер с полем построения изделия размером 150 на 250 миллиметров. Это наш новый продукт с достаточно демократичной ценой, мы его сейчас выводим на рынок. А к концу года представим на рынке самую большую нашу машину — с полем печати 500 миллиметров по стороне, это уже будет серьезный принтер промышленного класса. Разумеется, на конечный результат работают не только инженеры, а все подразделения компании, от производства до отдела продаж.
Так вот, о кадрах. Что касается наличия научного потенциала в нашей компании, то он у нас присутствует в большом объеме. Фактически все наше руководство имеет ученые степени докторов и кандидатов наук. В компании много ученых, ведь длительное время мы занимались в основном ниокровской деятельностью. Для аддитивного направления кадры мы преимущественно воспитываем сами. Где-то студента толкового вытащим, и через полгода-год он управляется с тремя станками разом, где-то с конструктором повезет или с программистом. Но все компетенции у нас внутри, мы их развиваем и бережно храним. К сожалению, извне аддитивных компетенций вместе с кадрами приходит не очень много.
Алкорамки, облакомеры и лидары
— У вас есть и другие серийные продукты в каталоге — чем они интересны?
— Наряду с 3D-принтерами нашим флагманским продуктом, который и сейчас в продажах компании занимает более 50 процентов, являются системы промышленной безопасности, экспресс-тестеры с технологией моментального выявления алкоголя в выдохе, так называемые алкорамки. История их появления тоже связана с выполнением одной из научных работ по созданию системы дистанционного мониторинга алкоголя в воздухе. Получив наработки, которые мы долго и мучительно формировали, пришли к выводу, что можно создать такой продукт, которого на рынке просто нет. Да, это банальный алкотестер, но не такой, как у сотрудников ГАИ, где нужно дуть в трубочку. Отличительная особенностью наших алкорамок заключается в том, что они работают не на электрохимии, а на оптической абсорбционной спектроскопии. То есть там нет никаких химически чувствительных элементов, там есть свет, который определенным образом взаимодействует с молекулами спирта в выдохе человека, и на основании этого взаимодействия мы делаем анализ, сколько там спирта в количественном содержании.
Результат алкорамка выдает весьма точно, время реакции составляет порядка полутора-двух секунд. То есть от выдоха к выдоху, от человека к человеку устройству достаточно двух, максимум трех секунд. Это значит, что пропускная способность проходных на предприятиях может быть очень высокой. Представьте, приехала смена на завод, две с половиной тысячи человек. Даже при наличии двух десятков турникетов, если все будут дуть в трубочку и ждать 30 секунд ответа, то только к концу дня смена пройдет проходную. Естественно, это недопустимо, а наша алкорамка позволяет такую проблему решить. Заказчики прониклись этой технологией, спрос на алкорамки стабильный, несколько тысяч алкорамок у нас по России стоит. И это продукт недешевый, но он окупается своей производительностью.
— Если алкорамка столь эффективна, почему не сделать нечто подобное для ГАИ?
— У сотрудников ГАИ нет необходимости в столь быстрой реакции, не суть важно, будет человек дуть в трубочку десять секунд или две секунды, можно и подождать. Хотя с другой стороны, мы сейчас разрабатываем продукты для муниципального транспорта и уже переходим к этапу их тестирования. Это будут портативные алкотестеры, которые интегрируются в автомобиль и без авторизации водителя, без осуществления выдоха водителя и замера алкоголя в воздухе не дадут завести машину. Тема актуальна для муниципального транспорта, может быть для каршеринга. Вот такие приборы можно ставить и работникам ГАИ, но пока особого интереса здесь нет, потому что прибор относительно дорогой.
— Кроме алкорамок какие еще продукты выводите на рынок?
— Есть у нас еще ряд серийных уникальных продуктов, которые, к сожалению, сейчас не сильно популярны из-за отсутствия нормативной базы. Это лидары для метеорологии и обеспечения безопасности полетов авиации. Лидары-облакомеры с помощью света детектируют состояние атмосферы, могут мерить нижнюю границу облачности, верхнюю границу облачности, плотность облачных слоев, их количество, высотность. Облакомеры — это относительно простые лидары, они необходимы для обеспечения безопасности полетов, то есть это работа аэропорта и вся сопутствующая метеорология.
Есть лидары более интересные, сложные, уже с доплеровским измерением, то есть они позволяют мерить все то же самое плюс еще направление и скорость ветра, причем на разных высотах. Ну и самая флагманская модель позволяет измерять по лучу на расстоянии до 10 километров направление и скорость ветра. В приземном слое детектирование опасных метеоявлений достаточно важно для обеспечения безопасности посадки. Вот, например, сдвиг ветра: когда на разных высотах вдоль посадочной глиссады ветер дует в разные стороны. Это опасно: самолет, идущий на посадку, может резко отклониться от курса. Известно много авиационных происшествий из-за сдвига ветра. С учетом того, что самолет постепенно снижается, проходя все эти горизонты ветра, его может занести, унести и пилот просто не успеет отреагировать на этот маневр. Так вот, если есть сдвиг ветра в глиссаде посадки, то такие данные пилоту необходимо знать.
Есть еще одно направление лидарной техники, которое сейчас в активнейшей разработке. Это лидары другого класса, это сенсорика, по сути дальнометрия. Мы разрабатываем лидары фронтального обзора для беспилотного транспорта — для поездов, метро, шоссейной техники, магистральных тягачей и так далее. Это лидары высокой детализации, но фронтального обзора. И еще один продукт в разработке — лидарная система для сферического обзора, для геодезии и 3D моделирования окружающего пространства. Прямых аналогов российского производства у нас в стране нет. Есть аналоги европейские, аналоги китайские, но ниша пока что свободна для российского оборудования.
— Полагаю, что и это еще не все направления вашей деятельности…
— Основные все назвал. Есть еще направление по космическим исследованиям. Но это не серийная продукция и вряд ли серийной станет. Это разработка научной аппаратуры для использования на борту МКС, для космонавтов. Здесь примерно такая логика: ученые, к примеру из Академии наук, ставят задачу провести тот или иной эксперимент в условиях микрогравитации, то есть космоса. И надо воплотить в жизнь желание ученых — в виде конкретного устройства, которое можно отправить на МКС для проведения там экспериментов. Этими задачами у нас занимается отдельный департамент, имеющий соответствующие компетенции и лицензии.
— Ваша компания под санкциями работает?
— Конечно. Но ничего страшного, у нас полстраны под санкциями. Что касается зависимости от импорта, то она небольшая, это не критические позиции. Более того, по последней нашей сертификации старшей машины в продуктовой линейке мы набрали 26 баллов из 26 возможных по системе Минпромторга, что подтверждает высокую степень локализации производства, дает преимущества при участии в конкурсных процедурах, доступе к субсидиям, налоговым льготам. А в Государственной информационной системе промышленности (ГИСП), которая была запущена Минпромторгом РФ в 2016 году как единая цифровая площадка для предприятий и позволяет без посредников реализовывать свою продукцию, мы находимся более двух лет. Конечно, конкуренция в области аддитивных технологий есть и с другими отечественными предприятиями, но это здорово, что такие современные технологии у нас в стране появились, рынок растет, и места хватит всем.
— То есть для укрепления своих позиций в аддитивных технологиях вам остается только масштабироваться? Что для этого необходимо?
— Да, в этом году мы законтрактованы на производство до конца года, а в следующем ожидаем кратного роста, планируем сделать не менее сорока принтеров, часть из которых — машины начального уровня и до половины — старшие промышленные установки, начиная с моделей М-450-М и М-450-S. Такое расширение потребует от нас как привлечения инвестиций, так и увеличения штата, производственных мощностей. И эта работа уже ведется. Мы участвуем в программах субсидирования от государства, привлекаем частные инвестиции, работаем с различными финансово-кредитными учреждениями. Уже пользуемся облигационными инструментами, планируем привлечь несколько сотен миллионов рублей, а полученные средства как раз и будут инвестированы в серийное производство 3D-принтеров. Есть планы и по расширению площадей, так как практически уже всю территорию комплекса освоили под производство. У нас амбициозные планы, мы верим в правильность принимаемых решений, и практика показывает, что мы правы.
Свежие комментарии